Page updated / checked 2.1.2025.
The share of value creating time in relation to the total elapsed time is typically very low in operations: often <10% or even <1% of the time. Lead time reduction is an important part of process improvement: it leads almost automatically to the question how to remove unnecessary tasks, waste, as well as waiting time from different processes. Looking for lead time reduction opportunities helps us to focus our improvement actions.
Reducing lead time through eliminating waste and waiting times means also that the process will be in better control: through lead time reduction also the variation of the lead time can be reduced. Thus there is a double positive impact from the customer’s point of view: on top of shorter lead times, the delivery accuracy typically also improves.
There are at least three key processes / flows which should be a target for lead time analysis and reduction:
- Order to delivery process, i.e. from the moment the customer makes an order (or wants to make an order) to the point when the product / service is delivered to customer and is ready for use. Order to delivery process can be thought of as the customer’s “window” into our company: speed in this process is seen directly as speedy delivery in customer’s eyes.
- Material flow throughout the whole supply chain. The speed in material flow brings many benefits: fast delivery times to the customer, fast reaction to changes in demand, low tied capital, and fast noticing of quality mistakes and other problems.
- New product development process or in big picture the whole process of bringing a new product to the market. By speeding up this process one can either be earlier in the market with the new product than the competition, or by starting the development later can utilize newer technology than competition, still coming to the market the same time than the competition.
In order to reduce lead times one must first understand how long the lead time is, how big is the variance in the lead time and how the total lead time is split between different steps of the process. In other words, one must map the process, measure the total lead time and its variance, and measure the lead times of individual steps. To find reduction potential, the process steps and individual tasks can be analyzed from four different points of view: can the task be removed totally, can tasks be combined, can tasks be speeded up (for example through eliminating waiting or automating), or can tasks be done in parallel.
Example of lead time reduction: Order to delivery -process
The company X had as a target to reduce the delivery time experienced by the customer, i.e. the lead time of the order to delivery -process. The process was first mapped together with the people working along the process. Time stamps were extracted from the IT systems and thus both the overall lead time as well as the lead times of individual steps were analyzed.

Could any of the process step be eliminated? Initially it was thought no, until someone came up with the idea of moving from make to order -production into assemble to order -production at least with some products. Of course, the parts manufacturing would not cease to exist, but it would be removed out of the critical path, i.e. the delivery time experienced by the customer. This is actually a common situation: we may not find steps that can be fully eliminated without compromising the end result, but removing can also mean that a process step is moved away from the critical path and carried out off-line from the time critical process.
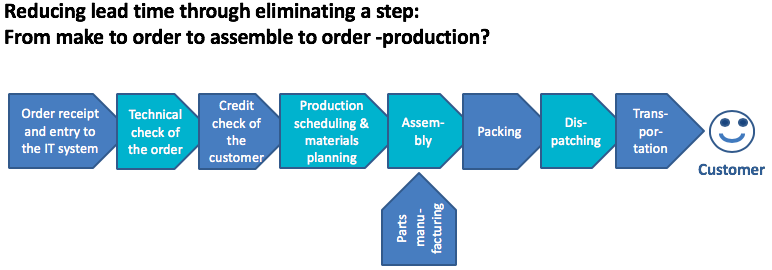
Could steps be combined? The representatives of production suggested that the packing could be done with the assembly. Thus two steps could be done on one go, eliminating the changeover time of finishing and getting started again, which would speed up the whole process.

What about carrying out two or more steps at the same time in parallel? The customer service team pointed out that the technical check and customer credit check are independent of each other, and they are done by different teams. Therefore they could well be done at the same time, in parallel.

Making an individual step shorter (faster) makes us usually think of carrying out the work faster. Speeding up how the actual value adding tasks are carried out is actually seldom the best solution – or even possible at all. Making an individual step faster usually means either eliminating waiting tasks within the step, eliminating unnecessary tasks within the step or automating tasks. In this example both waiting time elimination and automation were considered potential: the production planning could create and update the daily production schedules faster, if a more automatic scheduling tool which required less information re-entry would be taken into use. Additionally a further investigation was initiated to find out, why the customer orders waited quite long before production, and whether this waiting time could be reduced.

Even though each of the individual reductions were quite small, from few hours to some days, the did add up to a reduction potential of over one week when the process was analyzed in a holistic way from different angles.

The next task in Company X was to tackle the lead time variations in individual process steps. Small individual variations may accumulate to large overall variation. This in turn makes it impossible to make reliable delivery time promises.